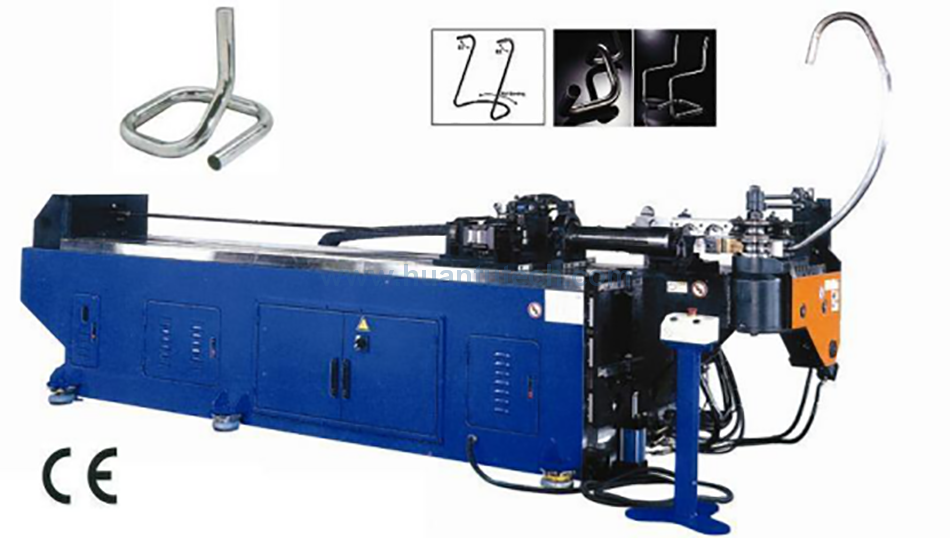

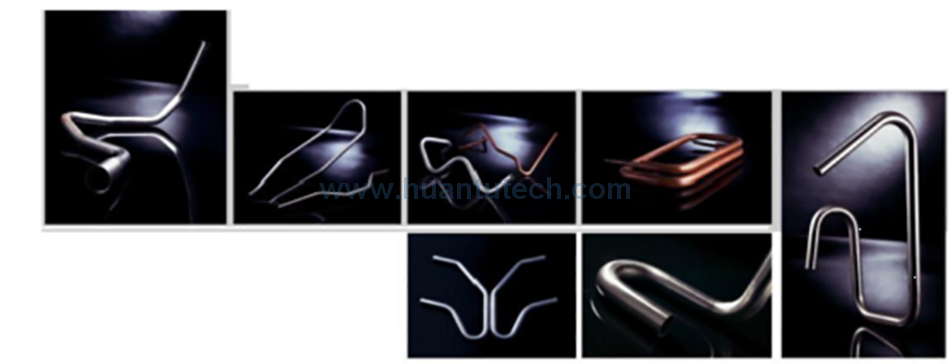
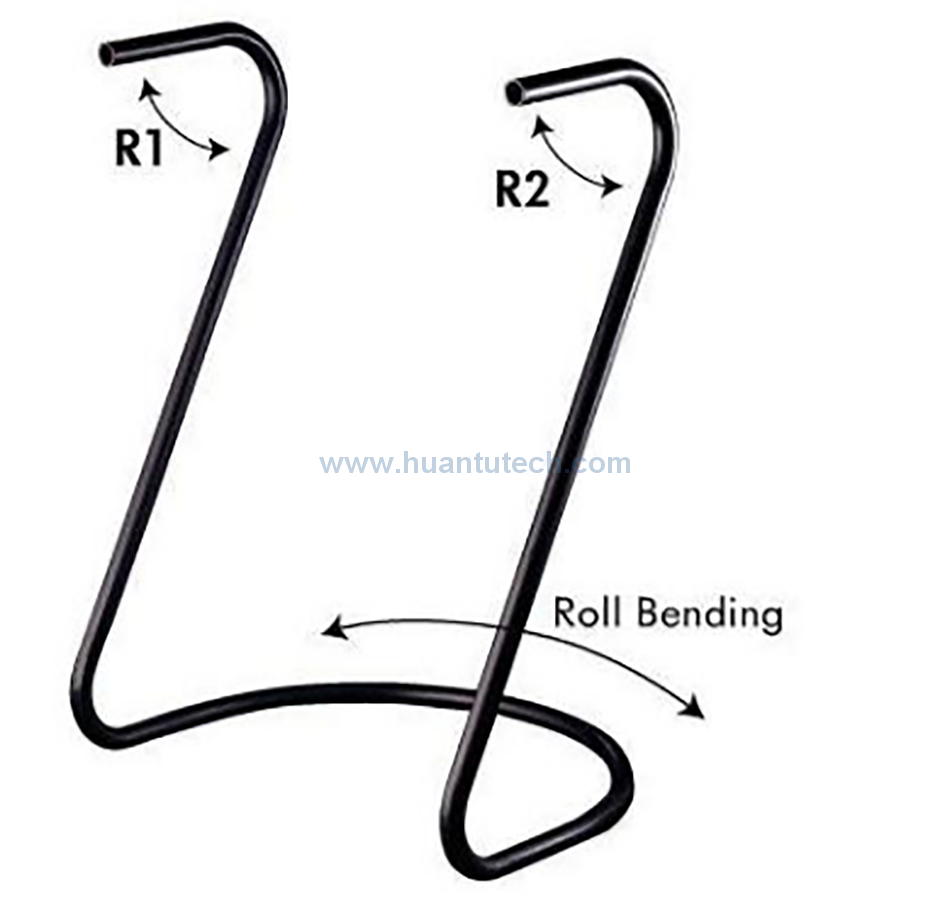
Technological parameter.
Item
|
Name
|
Unit
|
Data
|
remark
|
1
|
Max bending capacity
|
Round pipe
|
mm
|
Φ38×2t
|
Bending the samples as your drawings is single 1 step,we provide 3 samples ,but shipping freight is freight collected
|
Solid Round bar
|
Φ22
|
Square pipe
|
Φ32 X 32mm
|
Solid Square bar
|
Φ20 x 20mm
|
2
|
Rolling Bending radius
|
Draw bending
|
Round tube
|
1.5D - 5D
|
Rectangular tube
|
2D - 5D
|
3.
|
Roll bending
|
Round tube
|
6D- ∞
|
Rectangular tube
|
7D- ∞
|
4
|
Max bending radius
|
mm
|
180mm
|
|
4
|
Max feeding length
|
mm
|
2500
|
Can according to customer’s requirement
|
5
|
Max bending degree
|
Degree
|
190
|
|
6
|
Control Panel
|
|
PLC +touch screen
|
|
7
|
Bending unit
|
piece
|
16
|
|
8
|
Working speed
|
bending speed
|
Deg/sec
|
150
|
|
Rotary speed
|
Deg/sec
|
200
|
Rotary fast will be dangerous
|
Feeding speed
|
mm/sec
|
1000
|
|
9
|
Accuracy
|
feeding
|
mm
|
±0.1
|
|
rotary
|
Degree
|
±0.1
|
|
bending
|
Degree
|
±0.1
|
|
10
|
Rotary servo motor power
|
W
|
750
|
Japan Mitsubishi
|
11
|
Feeding servo motor power
|
Kw
|
1
|
Japan Mitsubishi
|
12
|
Bending rolling servo motor power
|
Kw
|
5
|
Japan Mitsubishi
|
14
|
Oil motor power
|
Kw
|
4
|
|
15
|
Max storage units
|
group
|
2000000
|
Can enlarge according to requirement
|
16
|
Max pressure
|
MPa
|
12
|
Adjustable
|
20
|
Hydraulic control system
|
|
Magnetic exchange valve
|
Japan Yuken
|
21
|
Oil tank
|
L
|
110
|
|
23
|
Machine weight
|
Kg
|
1500
|
|
24
|
Machine size
|
mm
|
3860×800×1350
|
|
26
|
Delivery time
|
days
|
40 days
|
|
27
|
Warranty time
|
month
|
12
|
|
General Introduction
1.DW38CNC X 4A-2SV fully automatic pipe bending rolling machine with punching function,with PLC control system,4 servo for bending,rotary,feeding,horizontal module changing ,vertical modeling changing and pressure die . 5 layers tooling. Touch screen panel display English and the Language you required,have different bending degree prefabricate,dialogue operation,can choose manual ,semi-automatic and full automatic operation manual, portable pedal switch with start and emergency stop function.
2.have draw rolling bending function
3.multi axles working simultaneously.
4.one key back up of programs for USB or disk storage.
5.Security code for the protection the data setting and selected operation features.
6. manual step by step teach code for interference solution
7.diagnosis error immediately
8.To access to the history bending setting data to the facilitate study of malfunction with one set of tooling
9. All the parts of hydraulic system,control system,driver system and display system are imported from famous brand,with high accuracy,high efficient,suitable for mass production.
10.CNC fully automatic,have cubical space bending equipment,loading the whole bending process is automatic. The machine is convenient operation,stable performance and high safety factor. The machine is the ideal choice for the pipe processing.
Configuration (can according to the customer requirements)
Item
|
Supplier
|
Magnetic exchange valve
|
Japan Yuken
|
Spillover Valve
|
Japan Yuken
|
Servo motor
|
Japan Mitsubishi
|
Servo Driver
|
Japan Mitsubishi
|
PLC
|
Japan Mitsubishi
|
Feeding gear
|
Germany Atlanta
|
Touch Screen
|
Taiwan smart face
|
Vane Pump
|
NOVA(Sino-America Joint venture)
|
Linear guide
|
Korea SBC
|
Sealing element
|
Taiwan DZ-UN
|
Reducer
|
Taiwan PHT
|
AC contactor
|
France Schneider Electrical
|
Thermal overload relay
|
France Schneider Electrical
|
Fuse
|
France Schneider Electrical
|
Proximity switch
|
Japan Omron
|
Power switch
|
Taiwan Mingwei
|
Motor
|
Wuxi Taihu
|
Oil Pipe
|
Jiangsu Jiake
|
Some features
1. Automatic recognition of power in machine and work piece,the processing is both quick and good
2. Slow returning core,boosted by barrow,improving the appearance of the angle.
3.The whole operation is in the computer,simple,quick and correct
4. Pasteurized programming system: draw and modify on the stereo pipe image on the screen,makes the operation simple,quick and correct
5. Rebound test: comparison test on the features of lots of pipe materials
6. Single-step debugging function- a careful observe on the deformation of the pipe material during the trail manufacture of dies.
7. Automatic drawing of the graphics of dies-clear help to develop new products
8. Over-all inspection: hydraulic/electrical circuit/ driving systems,absence of phase in motors/inversion,voltage,temperature,oil pressure,and automatically diagnose the troubles
9. Passwords,keys,working hours/ recordings of quantities,are applied to management of production
Accessories
1.2 sets of tooling
2.tool box : 1 pcs
3.Operation manual : I sets in English
4.CD: 1 pc